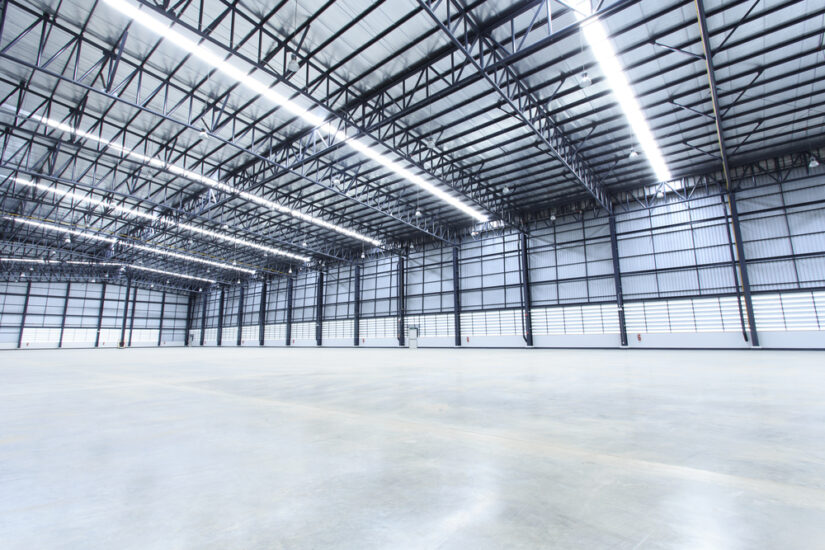
Discover the factors that impact warehouse costs and make informed decisions when building your storage facility. Trust US Patriot Steel’s expertise in warehouse construction.
Determining the cost of constructing or acquiring warehouse space is a significant concern for businesses looking to expand their operations or enter the logistics sector. US Patriot Steel offers an in-depth analysis of warehouse costs, factoring in the myriad of variables that can influence the final price. From the cost of raw materials to labor expenses, and from the location-specific costs to the customization of features, every aspect plays a crucial role in the overall calculation.
The comprehensive guide provided by US Patriot Steel addresses the key components that contribute to warehouse costs. It highlights the importance of understanding the cost implications of size and scale in warehouse construction. Factors like the price per square foot, which can fluctuate depending on regional market conditions, and the cost efficiencies associated with larger developments, are crucial for potential warehouse owners to consider.
Understanding Warehouse Costs
Warehouse costs are significantly impacted by a range of factors. Deciding whether to build or rent can alter financial commitments and operational flexibility.
Key Factors Influencing Costs
The cost to construct a warehouse is influenced by several variables. Location is paramount as land prices and building regulations differ widely. Size and scale of operations are crucial as larger warehouses require more materials and labor. Material costs can fluctuate, making metal constructions like those by US Patriot Steel an economical choice due to durability and maintenance benefits.
Comparing Building and Renting
Comparing the cost of building versus renting a warehouse involves a long-term perspective on financial commitments. Building a warehouse incurs high upfront costs but potentially lower monthly expenses. Conversely, renting can lead to higher operational costs but less initial capital investment.
- Building:
- Upfront Investment: High
- Long-Term Savings: Potential
- Customize to Needs: Flexible
- Asset Appreciation: Possible
- Renting:
- Upfront Investment: Low to Moderate
- Long-Term Savings: Less Likely
- Customize to Needs: Limited
- Asset Appreciation: None for Renters
Buildings may offer an opportunity to tailor the space to specific business needs, while renting could restrict customization but allow for greater adaptability to changing market demands. The decision should weigh current financial capacity against anticipated growth and operational stability.
Types and Construction of Warehouses
When considering the types and construction of warehouses, one must contemplate the variety of warehouse structures available and the impact of construction materials on the overall cost. The choice of warehouse type and building materials are decisive factors influencing the final price and functionality.
Different Types and Costs
Warehouses come in different forms, each designed to meet specific needs. The primary types include:
- Standard Warehouses: Typically used for general storage purposes.
- Automated Warehouses: Equipped with advanced technologies for efficiency.
- Climate-Controlled Warehouses: Necessary for temperature-sensitive goods.
- Distribution Centers: Optimized for quick turnaround and shipping processes.
- Flex Space: Combines warehouse with office or retail space.
Associated costs for constructing these warehouses vary due to their specific requirements. A breakdown of average costs is as follows:
Warehouse Type | Cost per square foot (USD) |
Standard | $50 – $80 |
Automated | $125 – $150 |
Climate-Controlled | $70 – $120 |
Distribution Center | $60 – $110 |
Flex Space | $55 – $95 |
Materials and Construction Impact
The choice of construction materials significantly impacts the final cost, durability, and maintenance needs of a warehouse. Key materials used include:
- Steel: Highly durable, offering long-term cost savings but with a higher upfront cost.
- Concrete: Offers robustness and thermal mass but can be costly and time-consuming to erect.
- Wood: Less expensive, but typically less durable than steel or concrete.
Each material comes with its inherent advantages and cost implications:
- Steel’s high durability leads to lower maintenance costs over time.
- Concrete’s thermal mass can translate to energy savings, despite its initial higher cost.
- Wood may lower initial costs but can lead to higher maintenance or replacement costs in the long term.
Constructing a standard 50,000-square foot warehouse, for example, will incur differing costs based on these materials:
By analyzing these factors, stakeholders can make informed decisions about warehouse construction that align with their operational needs and budget constraints.
Budgeting for Your Warehouse
When constructing a warehouse, precise financial planning is essential. The budget must encompass initial expenses such as permits and labor, as well as recurring costs associated with operations and maintenance.
Permits and Labor Considerations
Acquiring the necessary permits is the first step in budgeting. Local jurisdictions may require a range of permits, which can vary greatly in cost depending on the location, size, and purpose of the warehouse. These may include building permits, electrical permits, and zoning permits. In addition to permits, labor is a substantial expense. Costs are influenced by the project’s complexity, local wage rates, and the duration of construction. Skilled expertise is critical for specialized installations within the warehouse, further affecting labor costs.
Operational Costs and Landscaping
After construction, warehouses incur ongoing operational costs, which include utilities, insurance, security, and maintenance. Efficient operation of logistics facilities can minimize expenses, but they remain an unavoidable aspect of financial planning.
Landscaping, while often overlooked, impacts the budget. It involves not only initial setup costs for aesthetic and practical purposes (such as drainage and access roads) but also ongoing maintenance. Proper landscaping can in the long term help reduce operational costs by facilitating better drainage, reducing flood risks, and preserving access routes.
Operational Expenses | Factors Affecting Cost |
Utilities | Size of the warehouse, energy efficiency, local rates |
Insurance | Warehouse value, location risk factors |
Security | Size of the warehouse, location, type and value of stored items |
Maintenance and Landscaping | Size of the property, complexity of landscaping, local climate |
Each entity in the budget, from permits to landscaping, has a direct impact on the overall financial requirements of establishing and maintaining a warehouse.
Thorough evaluation of these costs is crucial for successful financial planning. Through tailored designs and a robust service offering, US Patriot Steel continues to be the preferred partner for businesses seeking efficient warehousing facilities.
We prove that steel construction can be seamlessly adapted to the specific needs of each client, reinforcing their commitment to excellence and customer satisfaction.